
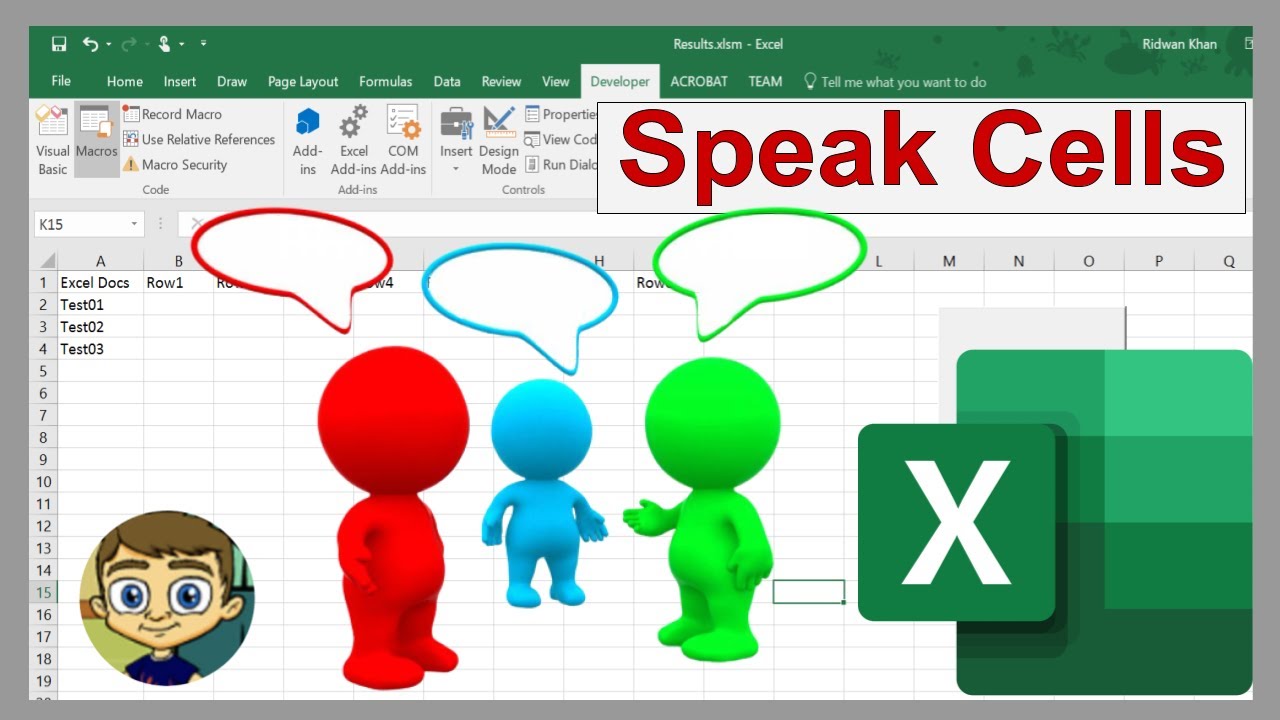
A failure mode has one or many potential effects. Failure Mode: The way that the process potentially fails to meet the requirement.The number and name should match with those in the process flow diagram. Process: Process step number and (or) process step name.The example of PFMEA Template body includes columns: Manager: the responsible person for releasing the FMEA document.Īs DFMEA Template, you can remove or add more fields in the header depending on what you need.Engineer: the responsible person for preparing the FMEA document.
#Excel for mac design mode code
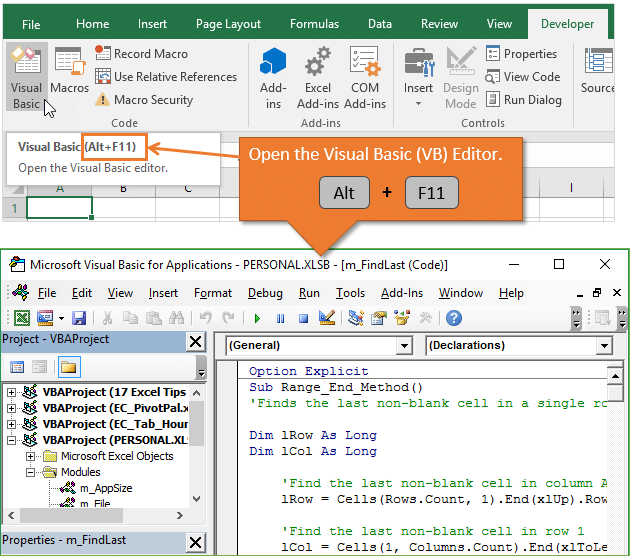
Responsibility: Individual person or team/department who has to complete the recommended action.Action: Recommended action to eliminate or reduce the chance of the causes of failure mode.Depend on RPN and S, O, D indexes, the responsible team/individual has to decide corrective action needed for each failure mode.

RPN: (stands for Risk Priority Number) An indication number to evaluate the risk of the process based on Severity, Occurrence, and Detection.Detection ranks on a 1 to 10 scale, 10 means worst detection capability. Detection (D): a ranking number reflects the best detection control method.Detection Control (in Control Method) Design action to detect the failure or the cause of the failure if it happens.Occurrence ranks on a 1 to 10 scale, 10 means the highest possibility of occurrence. Occurrence (C): a ranking number reflects the possibility of occurrence of the Failure.Prevention Control (in Control Method): Design action to prevent potential cause to occur.A failure mode has one or many potential causes. Cause: The reason why failure happens.Class: Special product characteristic or high-risk failure mode.Severity ranks on a 1 to 10 scale, 10 is the most severe risk. Severity (S): a ranking number reflects the most severe potential effect of a failure mode.Effects: Potential effects of the potential failure mode on the function and customers.Failure Mode: The way that an item potentially fails to meet the requirement.A requirement has one or many potential failure modes. Requirement: Requirements of a function.Items: Item (component, part, assembly) of the product/part to be analyzed.The information in the header can be customized to what you need to organize and control your document better. Revision Date: The latest revision date of FMEA.Original Date: The date that the original FMEA was compiled.Each organization should have a consistent document numbering system used for tracking the document.

